Chrystiano Araújo - University of British Columbia
Nicholas Vining - University of British Columbia
Zachary Ferguson - New York University
Enrique Rosales - University of British Columbia and Universidad Panamericana
Daniele Panozzo - New York University
Sylvain Lefevbre - INRIA
Paolo Cignoni - CNR ISTI
Alla Sheffer - University of British Columbia
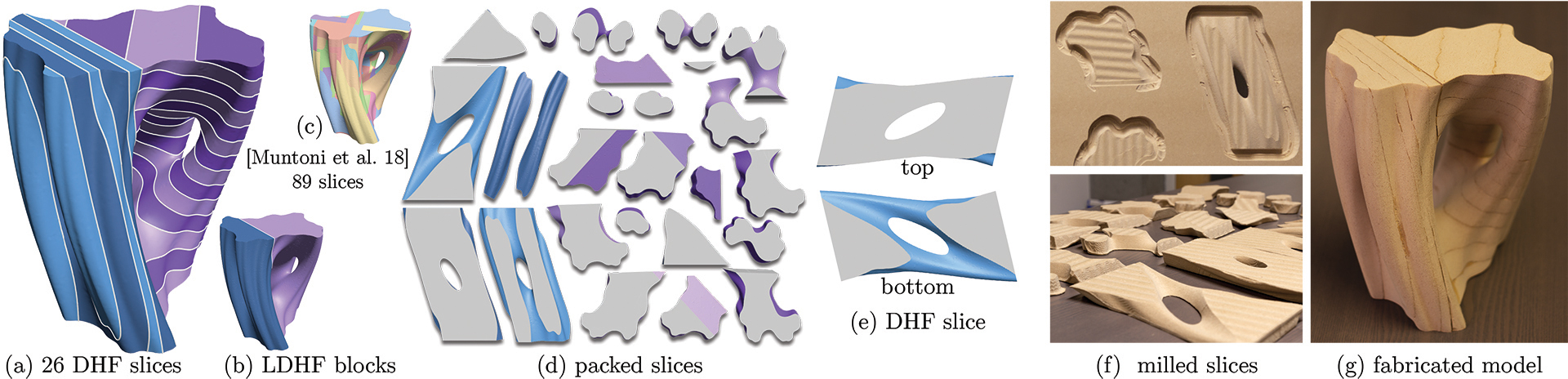
3-axis milling enables cheap and precise fabrication of target objects from precut slabs of materials such as wood or stone. However, the space of directly millable shapes is limited since a 3-axis mill can only carve a heightfield (HF) surface during each milling and their size is bounded by the slab dimensions, one of which, the height, is typically significantly smaller than the other two for many typical materials. Extending 3-axis milling of precut slabs to general arbitrarily-sized shapes requires decomposing them into bounded-height 3-axis millable parts, or slices, which can be individually milled and then assembled to form the target object. We present DHFSlicer, a novel decomposition method that satisfies the above constraints and significantly reduces both milling time and material waste compared to alternative approaches. We satisfy the fabrication constraints by partitioning target objects into double height-field (DHF) slices, which can be fabricated using two milling passes: the HF surface accessible from one side is milled first, the slice is then flipped using appropriate fixtures, and then the second, remaining, HF surface is milled. DHFSlicer uses an efficient coarse-to-fine decomposition process: It first partitions the inputs into maximally coarse blocks that satisfy a local DHF criterion with respect to per-block milling axes, and then cuts each block into well-sized DHF slices. It minimizes milling time and material waste by keeping the slice count small, and maximizing slice height. We validate our method by embedding it within an end-to-end DHF milling pipeline and fabricating objects from slabs of foam, wood, and MDF; demonstrate that using the obtained slices reduces milling time and material waste by 42% on average compared to existing automatic alternatives; and highlight the benefits of DHFSlicer via extensive ablation studies.
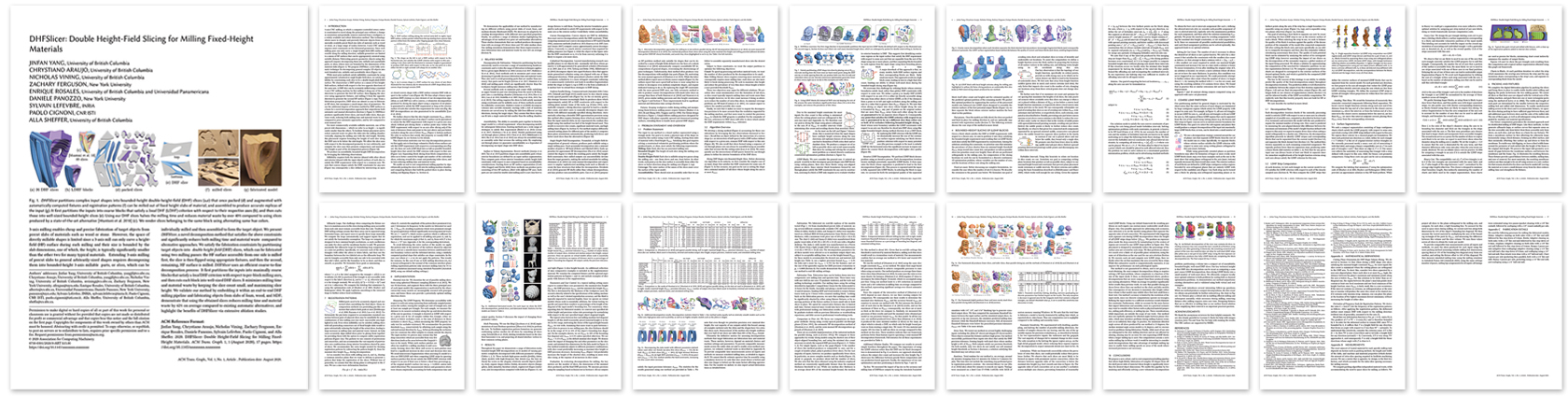
@article{Yang:2020:DHFSlicer, author = {Yang, Jinfan and Ara\'{u}jo, Chrystiano and Vining, Nicholas and Ferguson, Zachary and Rosales, Enrique and Panozzo, Daniele and Lefevbre, Sylvain and Cignoni, Paolo and Sheffer, Alla}, title = {DHFSlicer: Double Height-Field Slicing for Milling Fixed-Height Materials}, journal = {ACM Transaction on Graphics}, year = {2020}, volume = {39}, number = {6}, doi = {https://doi.org/10.1145/3414685.3417810}, publisher = {ACM}, address = {New York, NY, USA} }